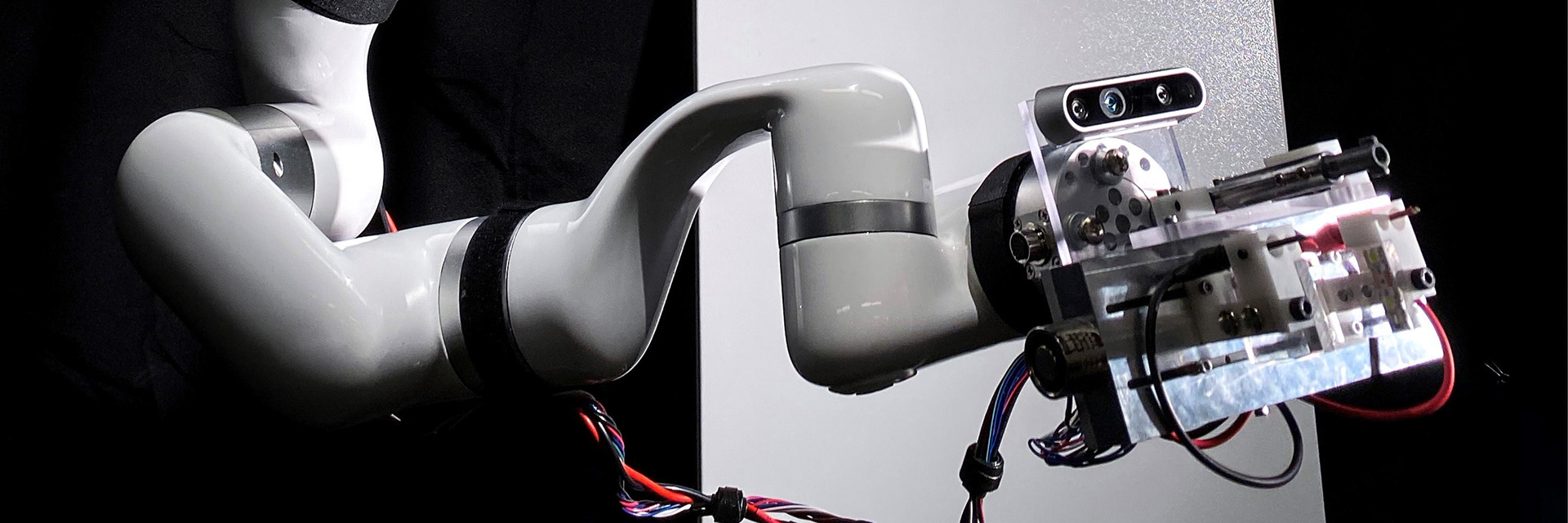
Offshore wind turbine maintenance is logistically challenging and requires skilled technicians. To reduce service costs and improve turbine reliability, our team partnered with Siemens Gamesa Renewable Energy (SGRE) to develop a robot for turbine diagnostics and service. This robot was designed to be installed inside the turbine where it would be remotely operated to perform remote electrical testing and verification. This would allow many simple maintenance tasks to be performed without requiring the time or expense of a human maintenance crew to travel to the turbine.
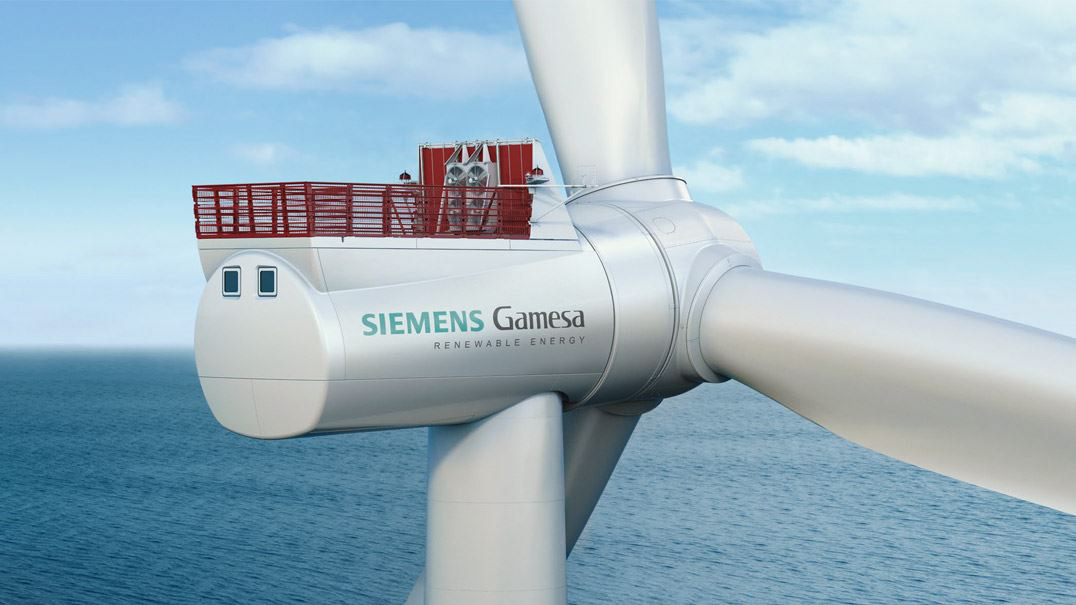
Our robot made use of overhead rails installed inside Siemens Gamesa offshore towers to traverse the interior of the turbine nacelle and access electrical cabinets. A powered lift system would then lower a 6-axis robot arm to the desired cabinet, and lock in place for finer control.
The user could control the arm remotely, and use a custom designed gripper to manipulate electrical components, use a multimeter to test electrical components, and press and release emergency stop buttons. We used a depth sensing camera to provide additional data to the user.
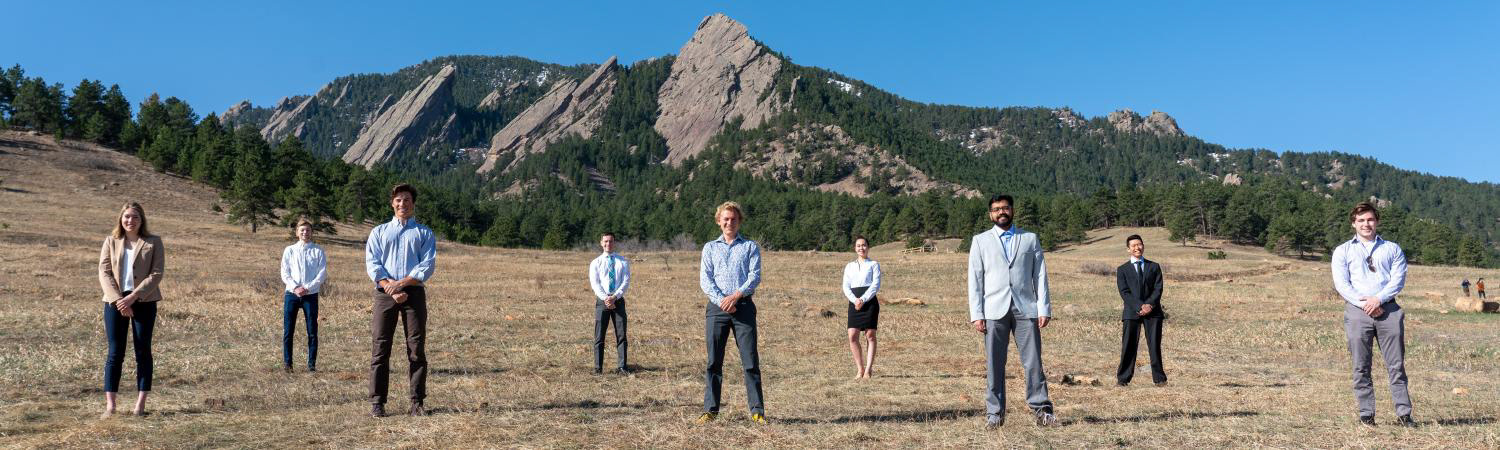
I served as Project Manager for a team of 9 senior engineering students from the University of Colorado Boulder's Mechanical Engineering and Electrical Engineering departments. I directed communication with the client, created and managed the project timeline, and designed and fabricated custom components. Our team delivered a functional final product that met or exceeded all design specifications.
At the end of this project, we delivered a working prototype and collaborated with engineers from Siemens Gamesa to inform the design of future turbines with service and diagnostic robots built in. The results of this project will help reduce the service costs of offshore wind turbines, and contributing to lower prices for renewable energy.
IMAGE GALLERY
PROJECT WHITEPAPER
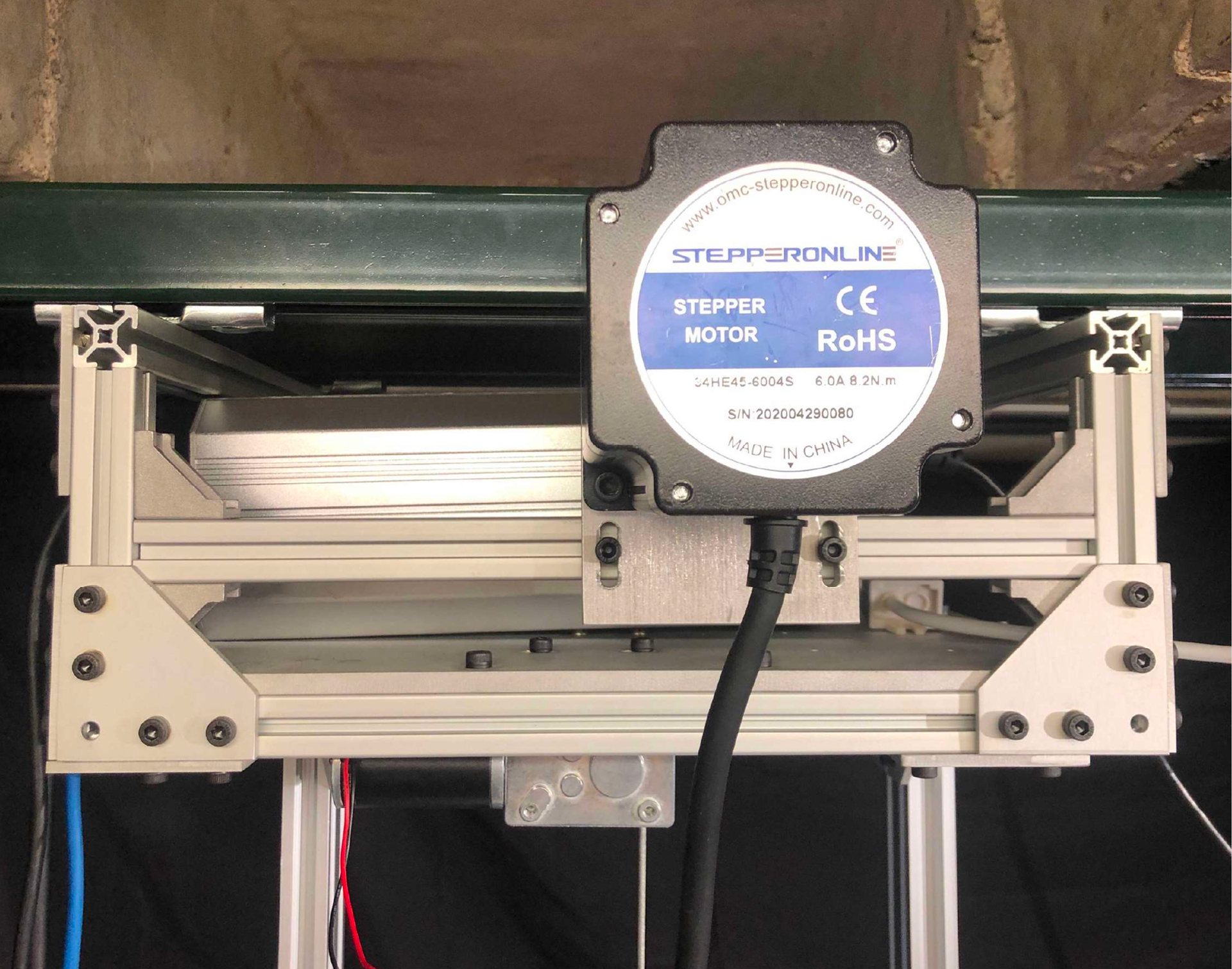
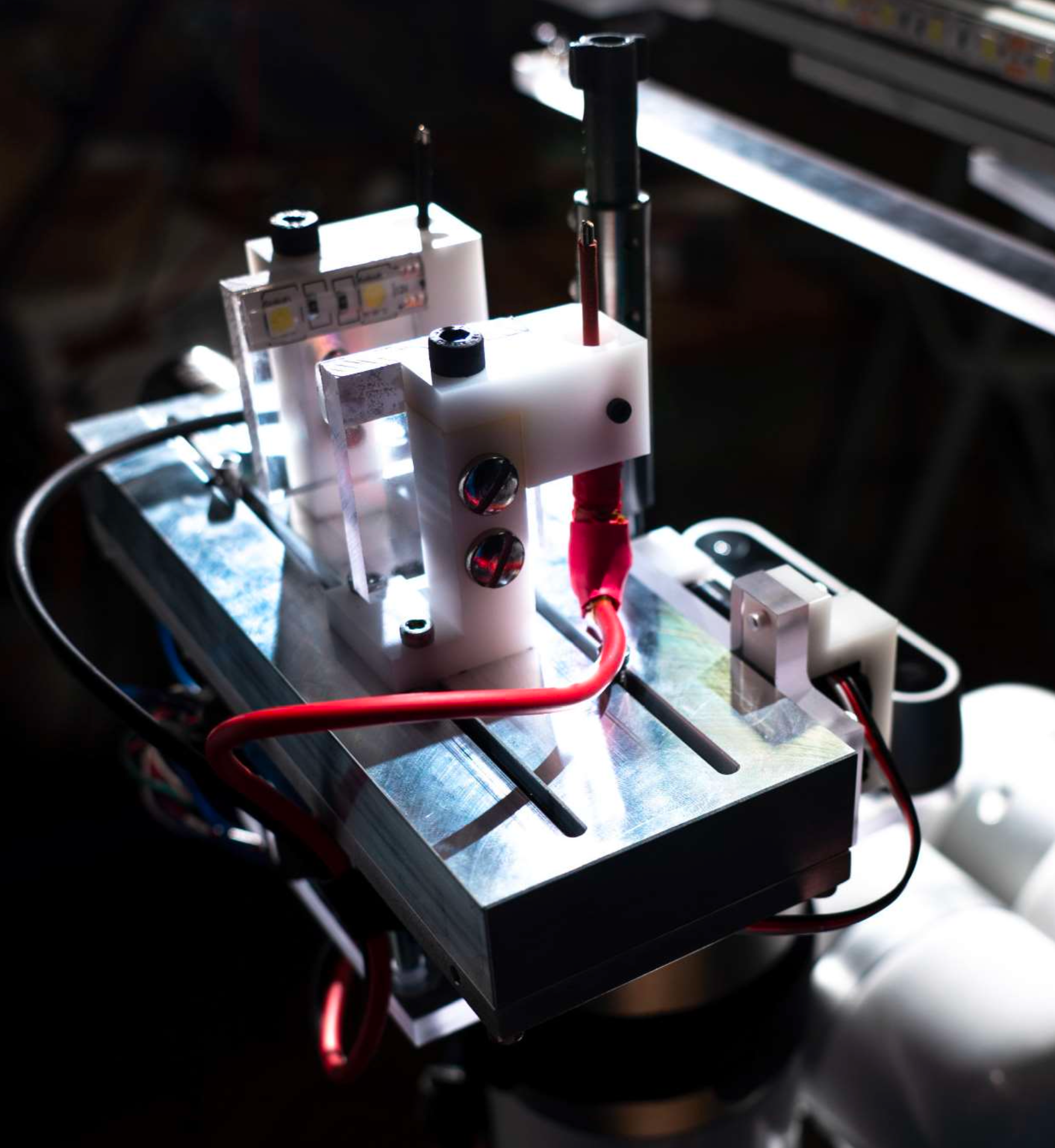
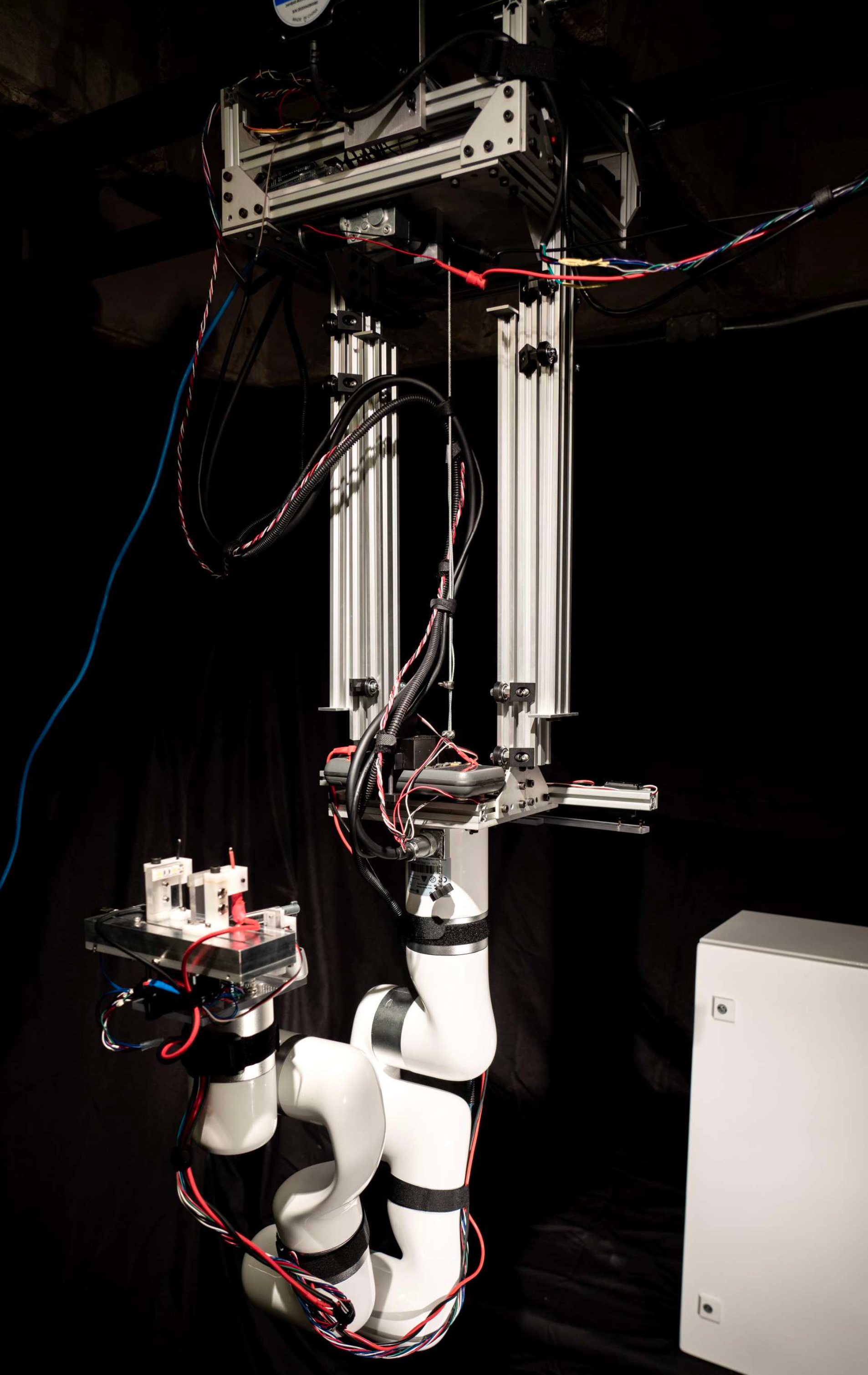
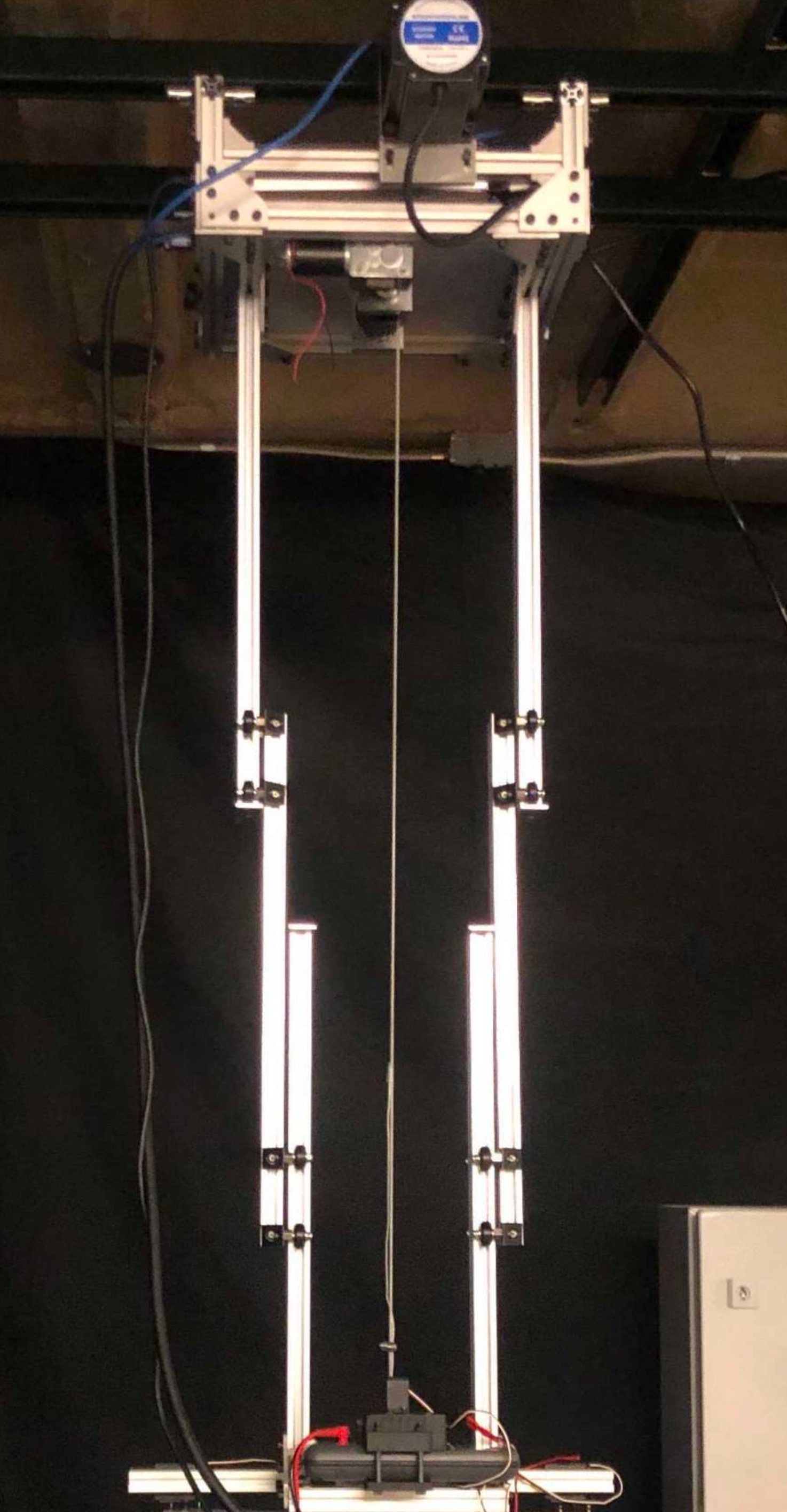
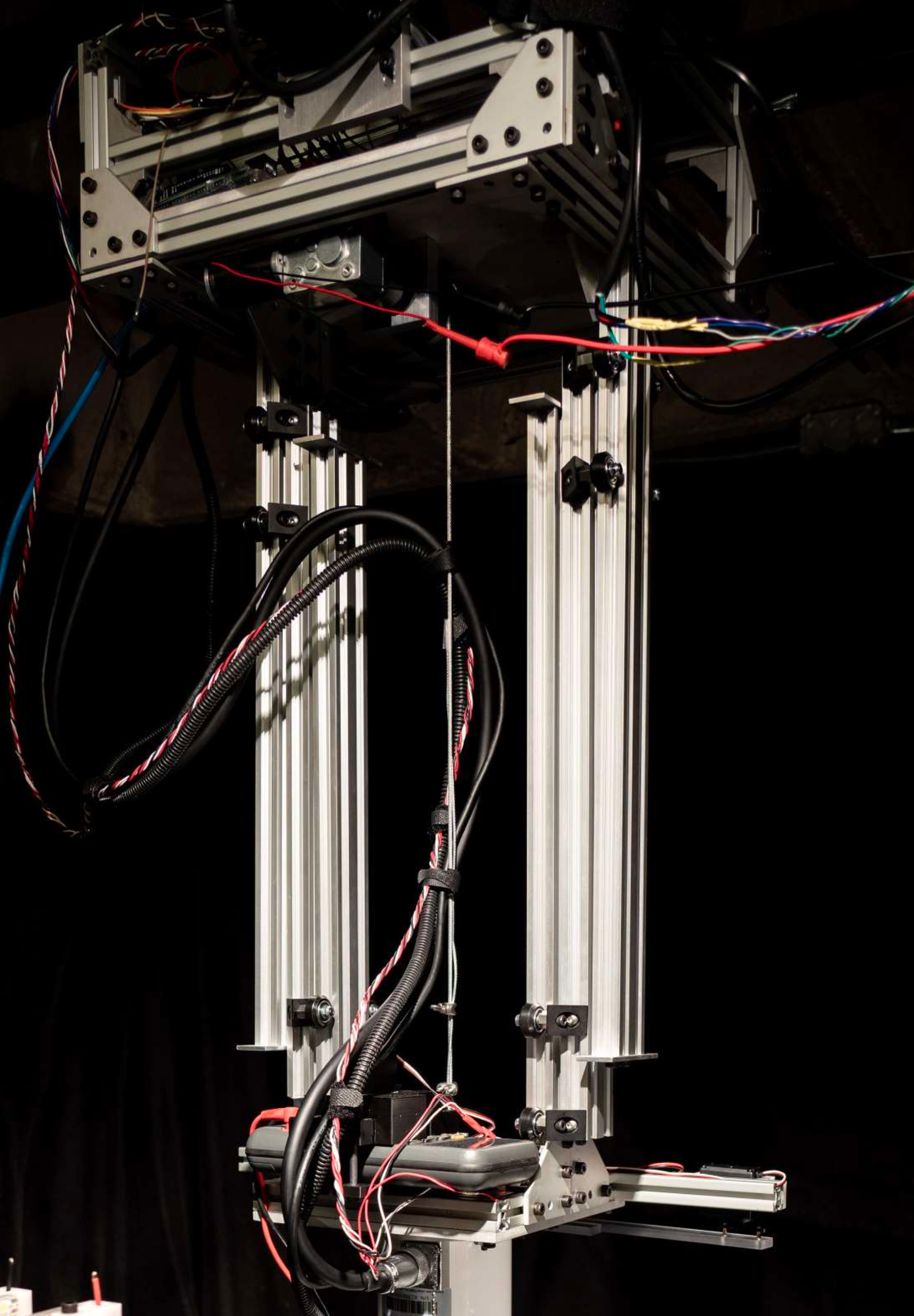
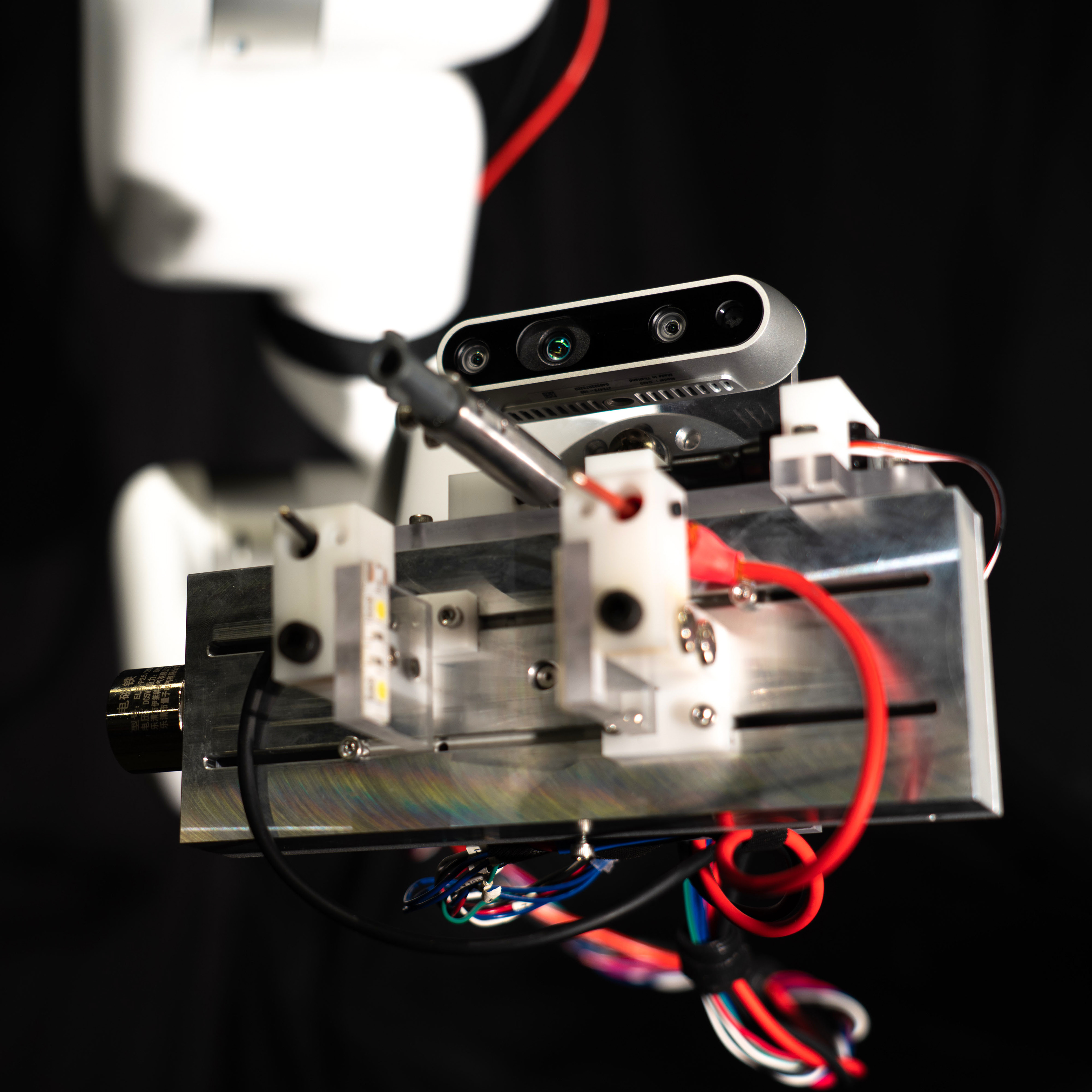
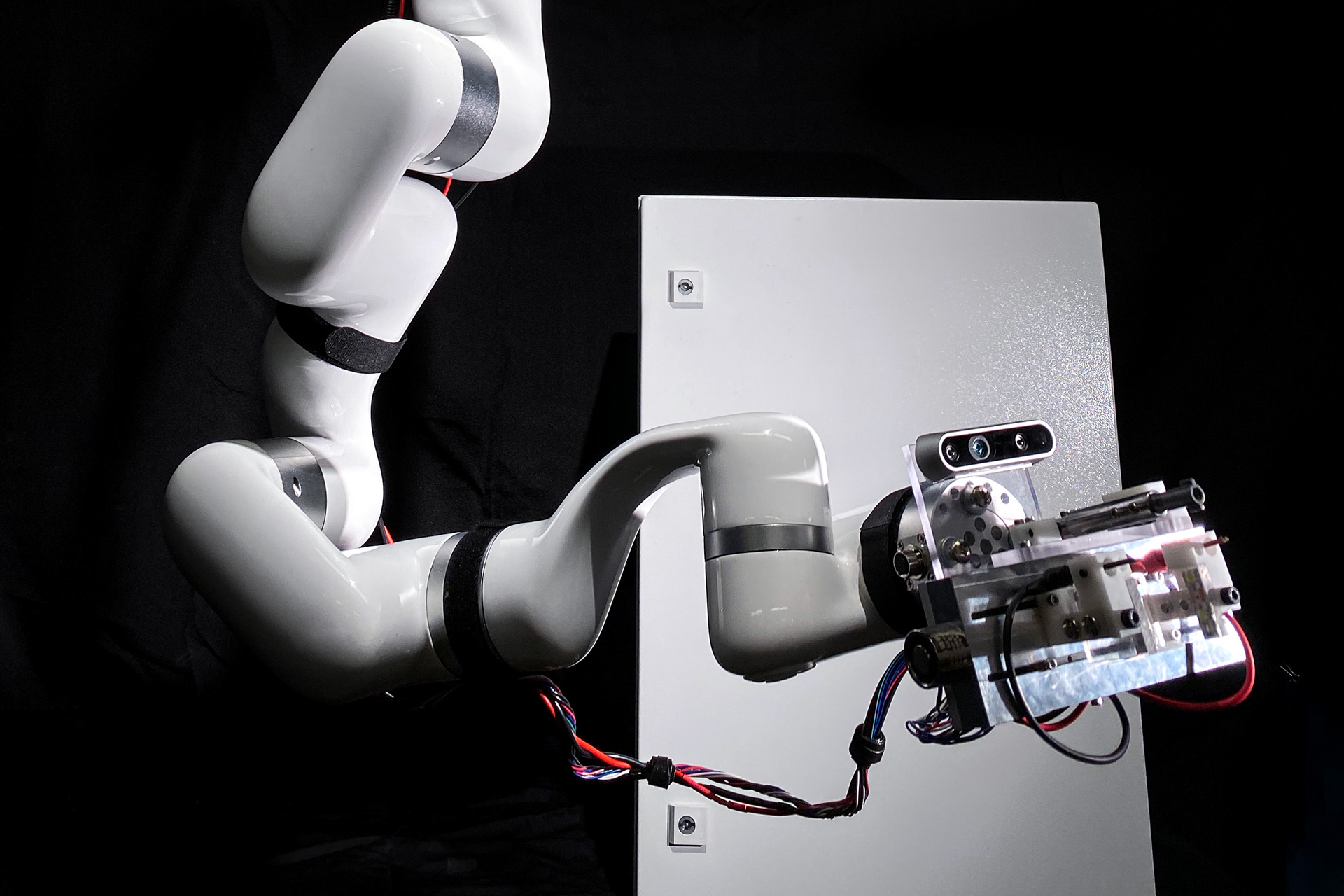